CARBON FIBER LAYUP ANIMATION
CARBON-FIBER PROJECT
The objective of this project was to understand the design and manufacturing process of laying up carbon-fiber parts using Ingersoll Machine Tool's Automated Fiber Placement Process. This was done by attempting to design and manufacture a carbon fiber part. This exercise provided insight that enabled optimization of the client experience.
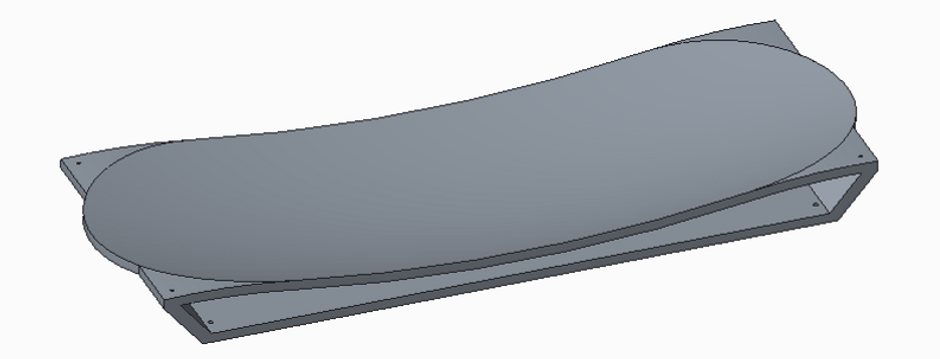
MOLD DESIGN
​

MANUFACTURING ASSEMBLY
An assembly of the final part, the mold, and the attachments required for mounting the mold.

MOLD PRINTING
The mold was printed with a unique 3D Printer. The nozzle size diameter is 1/2 inch. The material used to print the mold is Polyphenylsulfone (PPSU) with 10% chopped carbon fiber. This is so the mold can withstand the high temperatures used to cure the carbon-fiber part.
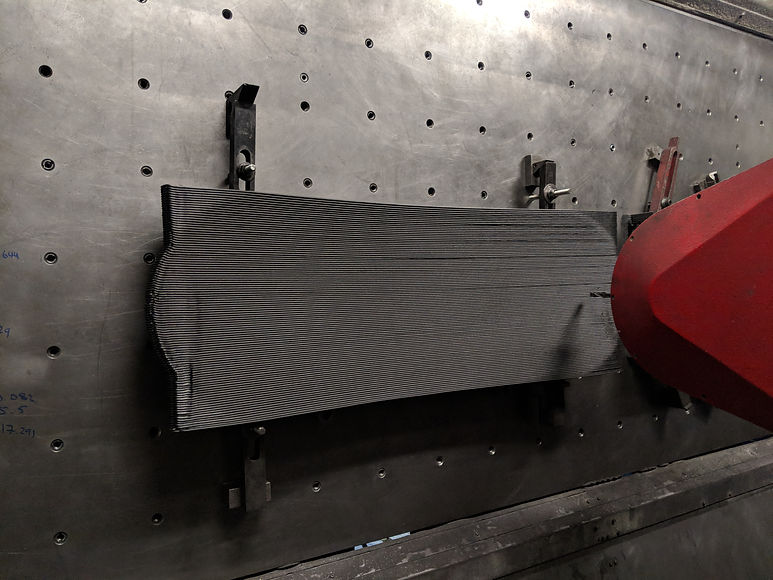
MOLD MACHINING
The extrudate width requires the mold to be machined to the actual size of the designed mold. Any errors due to the printing phase must be filled with an epoxy resin that can withstand high temperatures.

STACK SEQUENCE OPTIMIZATION
Altair's OptiStruct was utilized to optimize the stacking sequence of the various ply orientations.

BOUNDARY LAYER OPTIMIZATION
The stacking sequence was then applied to the part. The part was then run through another simulation to optimize the boundary layer for each ply. As shown, certain layers do not cover the entire length of the part. This ensures that the design criteria are satisfied and there is minimal material wastage.
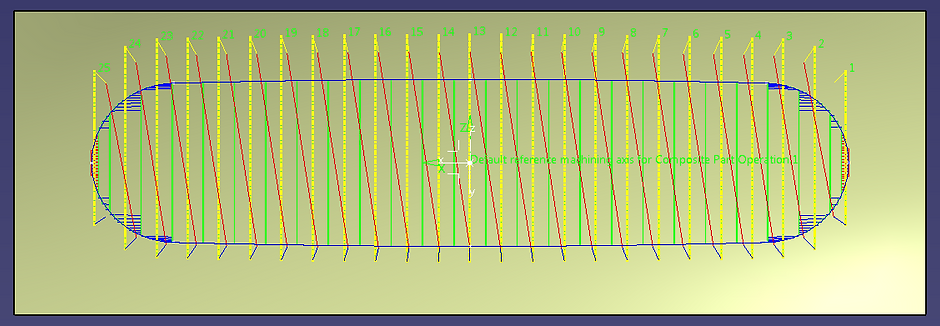
90 DEGREE LAYER TOOLPATH
This is an example of a tool path for laying down a 90 degree ply.
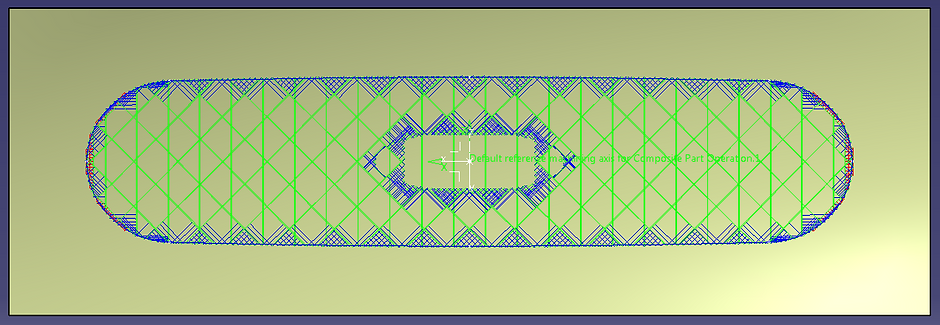
FINAL LAYUP
This is the final layup, the collection of all the tool paths required to create the final part.

FINITE ELEMENT ANALYSIS
​